“Process Improvement”
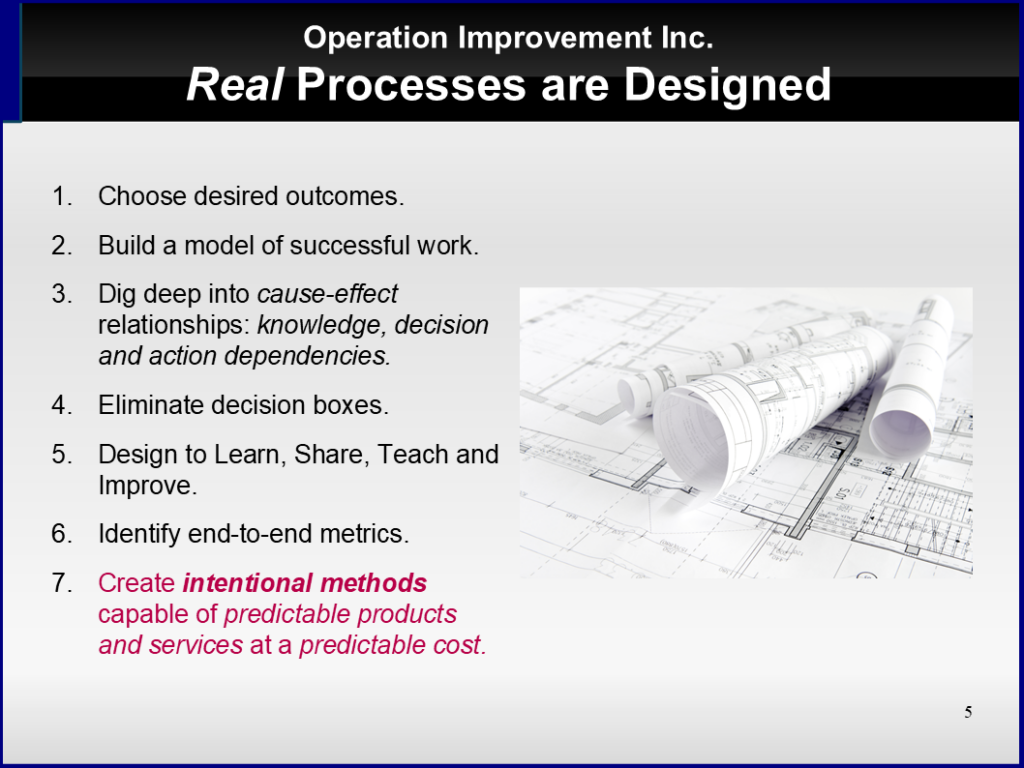
On a company walk-through, we observed a clerk trying to receive and read new customer orders on a remote CRT display terminal tied to the customer’s mainframe.
The clerk struggled to interpret the really old and coded “punch card” fixed field format. Then, the clerk would carefully type in the order for manufacturing on the company’s own in-house computer system.
The manager saw no problem with this process but thought that perhaps training would improve things a bit. It is likely that this order-intake/order-entry area would never have been targeted for “improvement” or flagged as a problem area. “If it’s not broke….”
Some processes don’t need to be improved. Some processes don’t have a problem that needs to be fixed. Some processes simply need to be eliminated.
What is often called for is a fresh look that is not prejudiced by how the work was previously done. Start with the objective. Don’t sub-optimize. Is the objective “improved” order-entry, or making it as easy as possible for the customer to place orders?
The very first step in process improvement is, “Show me everything. Let’s walk through the big picture.” Problems like the order-entry issue will then immediately stand out to a fresh set of experienced eyes.